Min Chun has an experienced engineering team, who in conjunction with the latest oversea automatic fixture technology, high-precision production equipment in variety, five-axis machining methods, tool matching and selection plus the innovative thinking of engineering, design process technology development, etc. may shorten development schedule by over 50%, reduce material expenditure, enhance production effect and lower human resources management costs, making it a high-efficiency and high-quality development model.
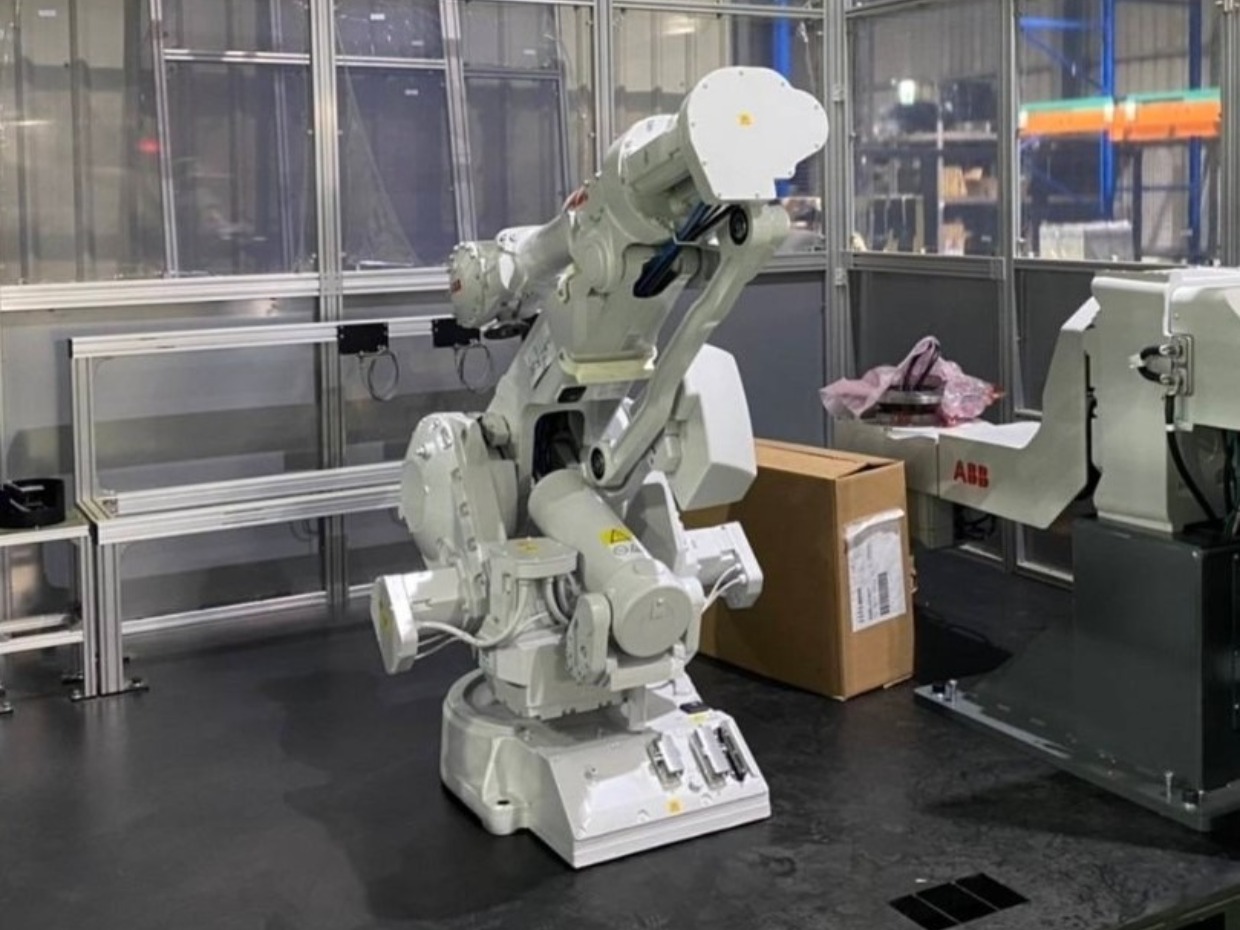
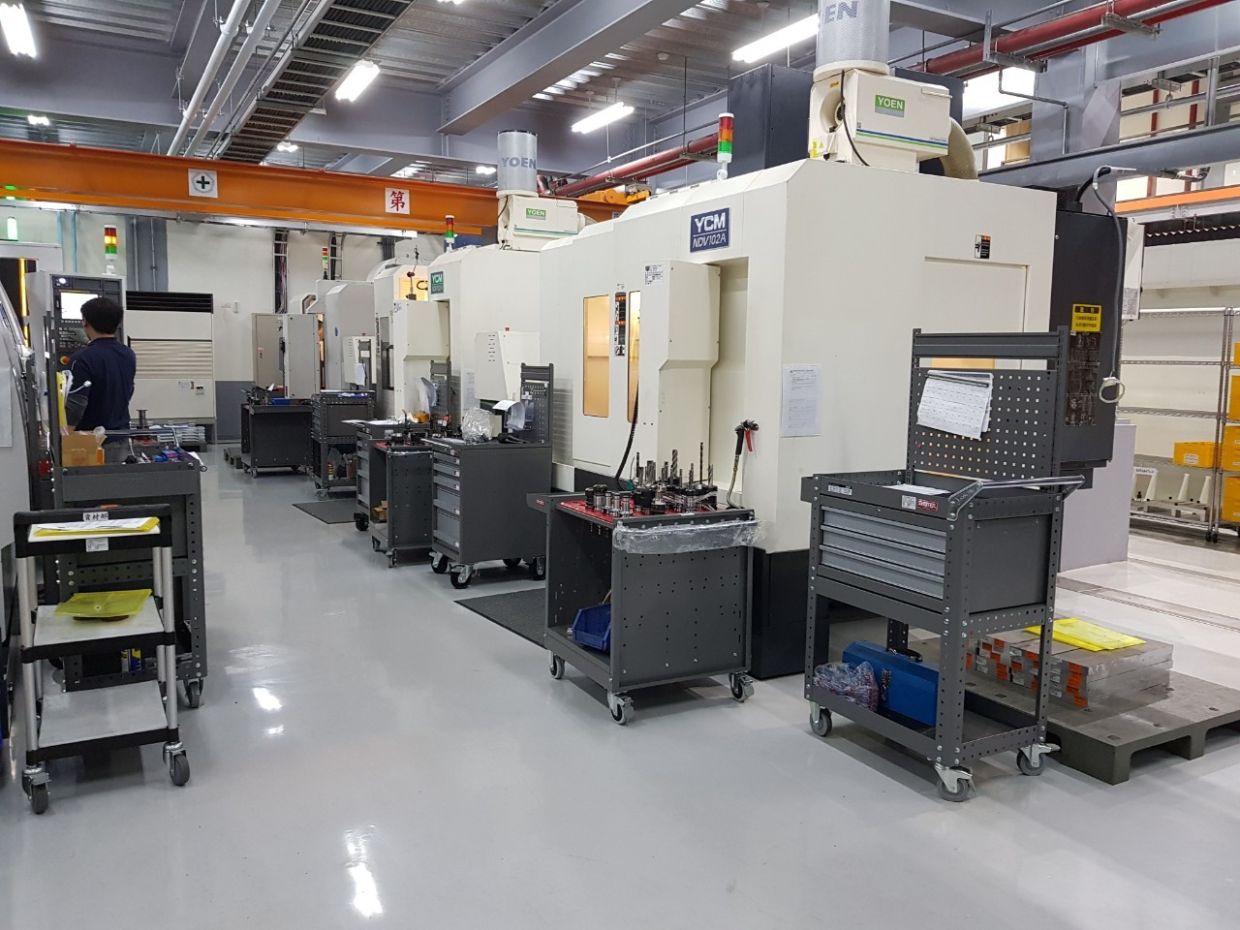
For the technology development of manufacturing process applied for hard-to-cut materials amongst aerospace parts, a production adhering to production management procedures is adopted, which not only ensures product precision and lead time, but also allows collection of engineering data intended for further analyses on real-time production information of various production equipment and loading of on-line milling and cutting, which may contribute to seeking optimal manufacturing conditions and discovering the root cause of anomalies for a mass production with greater efficiency and competitive edge.
Machine equipment details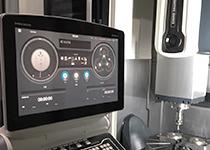
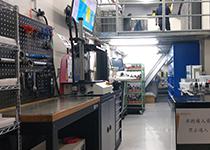
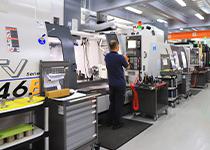
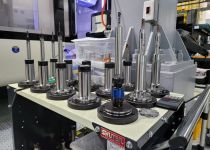

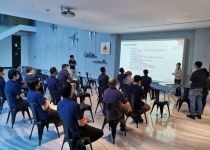
品質管理
iso9001
AS9100(D)
EGAT
qualified supplier
AIDC QUALIFIED SUPPIER
(S-200)
GE AVIATION QUALIFIED SUPPLIER
(T9669)
GE AVIATION holemaking Class A
(GT193)
GE AVIATION holemaking Class B
(GT193)
流程規劃
001
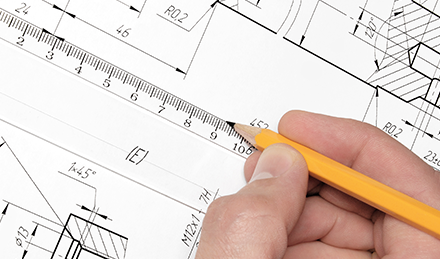

Inquiry & Business Stage
Inquiry & Business StageClient Drawing Inquiry → Negotiation on Project and Engineering Affairs → Contract Signing/Project Kick Off→ NPI Development
002
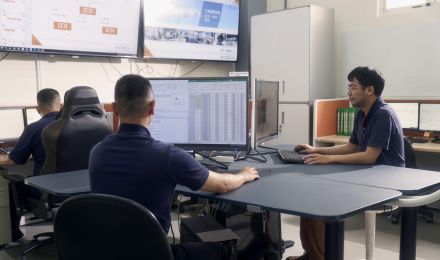

Product development stage
product development stageEngineering Interpretation of Detail Specification→DE : CAD→On Machine Development: CAM→Machining→Surface Treatment.
003
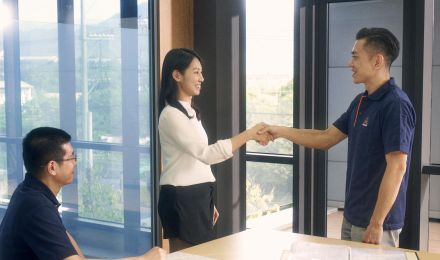

Customer confirmation stage
customer confirmation stageQC-First Article Inspection for Developed Product → QA FAI Document & Issuance of Quality Assurance Certificate
客戶服務案例
Completed the Development of Combustion Section Parts for New Aerospace Engine
The high bypass ratio turbofan engine developed by the customer is used on the Boeing 777X model. The engine is derived from the singular GE90 engine and will improve fuel efficiency by about 10%, and replaced the GE90 as the world's largest thrust aircraft engine in the Guinness World Records.
Min Chun manufactured high temperature combustion section parts, using Inconel 718 & 718 plus metal materials.
Completed the Development and Delivery of 108 Parts for Manufacturing Aircraft under the Indigenous Fighter Plane Program
The first AJT (Advanced Jet Trainer) new type of higher education aircraft officially left the factory at Taichung AIDC Co., Ltd. and named "Yongying". aircraft and F-5 training aircraft.
Min Chun mainly manufactures fighter main beam wing parts, tail control structural parts, fuselage cockpit parts, etc., totaling about 108 parts.